Table of Content
We have built on piers, as well as pre-existing foundations, and we have managed the most unfortunate situations when customers have lost their homes to a fire or storm. And, no matter which building method you choose, quality is your top concern. The nonprofit also focuses on building generational wealth and encouraging entrepreneurship. The chassis also incorporates a removable hitch, axles, and wheels. Most often, the hitch, axles, and wheels are removed upon mobile home delivery and installation to make way for siding and skirting.
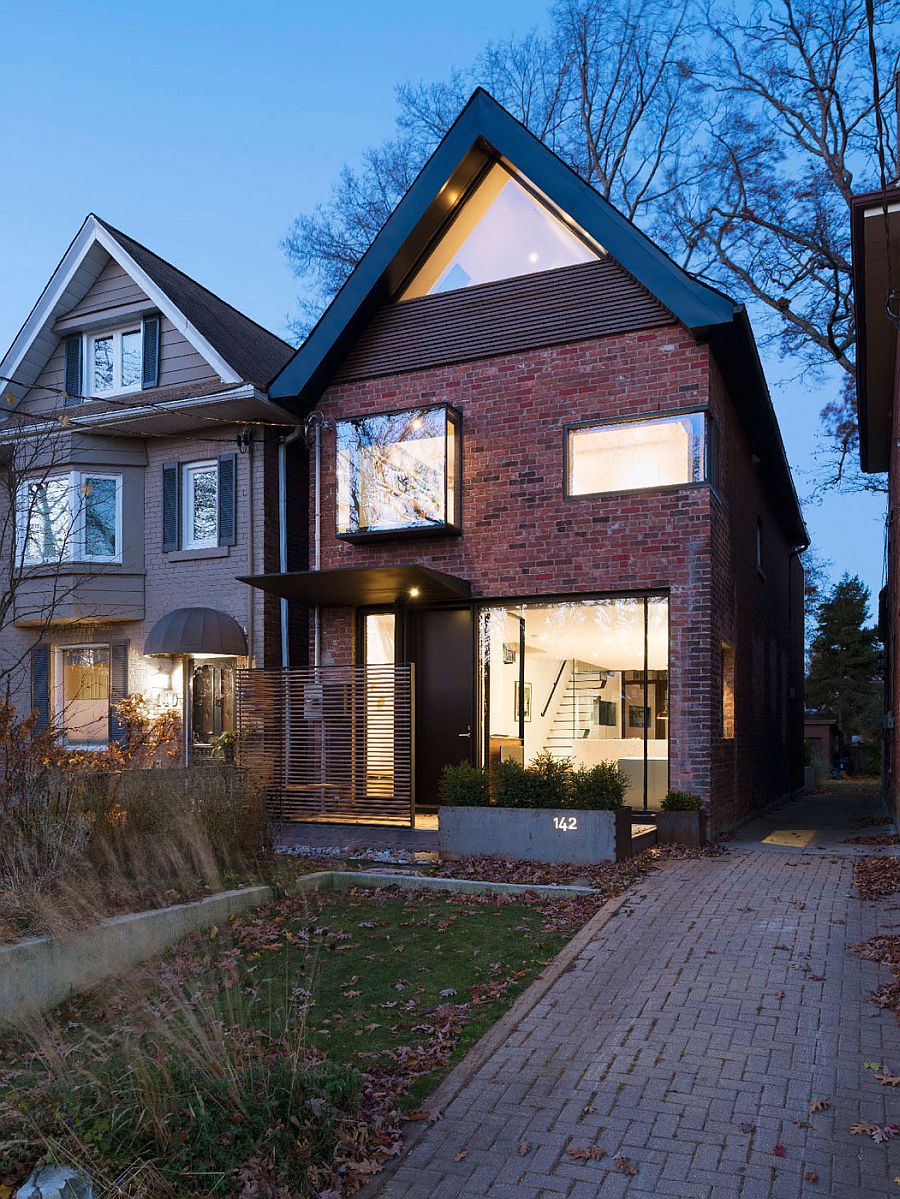
With literally hundreds of floor plans to choose from, we have the flexibility to completely customize your new home. Modular homes are stronger homes built under controlled conditions. Site built homes experience delays and damage to weather, a factor that cannot be controlled. Additionally, Virginia Modular Homes 1st can buy building materials in bulk, passing that savings onto you, while still maintaining our high building process standards.
Early 1900’s: Early Rise and Fall of Modular Homes
If a person wants to be a homeowner but they cannot afford to build a new home, a modular home is a great alternative. SIP panels, structurally insulated walls that could be locked together, were developed. The modular home became even more popular in 2003 when Dwell Magazine held a modular invitational. The idea was to mass produce homes that when erected on site, would look just like a traditional home. In 1908 after the Sears Roebuck Company was founded, they began selling kit homes. The original kit homes were the basis of the modular home idea.

This is not only because the cost of the permits is different, but also because some regions have an entirely different list of required permits than others. You can acquire a different list of required permits and their costs from your are’s town office, but this is a breakdown of the required permits for our home in Bethel, and their costs. Get in touch today and find out how we can bring your business more traffic from active home shoppers.
What Does a Modular Home Cost?
Instead, we just moved the home to a slightly different location, allowing us to avoid the hassle altogether. Since we want extra space for storage and the option to add more living space in the future, we went for a full basement instead of a crawl space. Placing the modular home on a crawl space would have been equally sound structurally and only half the price, but the utility of a full basement is a worthy investment.
If the home is to be moved, the axles and wheels are re-attached. Mobile homes became manufactured homes, by legal description, in 1976 when the U.S. Department of Housing and Urban Development began to ensure the safety of the homes, as well as the way they’re installed.
CLASP (Consortium of Local Authorities Special Programme)
Modular homes – also often known as factory-built, prefabricated, or systems-built homes – still only represent about 1.5% of all single family homes in the U.S. But more and more, the interest in modular housing is growing among American homebuyers. This is because modular homes offer both the flexibility to modify and create custom floor plans, as well as all the modern amenities, features, and design styles you’d expect in traditional homes. Our modular buildings are built to the same building codes as traditional site-built construction. Our structures can be placed on a variety of foundations, such as crawlspaces, pilings, or stilts. Affinity Building Systems is based in Lakeland, Georgia and provides modular buildings to independent, authorized builders throughout the Southeast.
Manufactured homes are built as either a single section home or a multi-section home, depending on the floor plan. They are constructed and delivered on a permanent chassis, so a permanent foundation is not necessary. Because of their efficient, high-quality construction, these homes provide the best value in home buying. Manufactured homes conform to Housing and Urban Development codes. It also prescribes performance standards for the mechanical, plumbing and electrical standards.
Modular Home Financing Has Never Been Easier
Square footage and selected options will often be the largest determiners of price point. Another large contributing expense, outside the cost of the modular home itself, is the land to put it on. Final installation and finishing expenses incurred by the builder or contractor must also be factored in. Affinity Building Systems uses the most sophisticated systems-built technologies to construct single-family, multi-family and commercial properties.

Modular homes, on the other hand, can be financed regardless of the year that they were built. When modular homes are built, they are built from the inside out. It typically takes just a few days to build one of these homes in the factory and there is an inspector there to make sure that during each step, the codes are being met. Also, buyers have more design and style options when they have a modular home built than if they were to purchase a manufactured home.
In-plant inspectors as well as independent agencies inspect your home on behalf of federal, state and local governments for code compliance. Evidence of this inspection is normally the application of a federal, state or inspection agency label of approval. Once the whole volume is tightened together, the installation of the chosen waterproofing system takes place as well as the installation of doors and windows. All doors and windows will be properly fastened and sealed to avoid the infiltration of both air and water. While some manufacturing companies will choose to waterproof the entire exterior including walls, floor and roof; others will only waterproof the roof and the exterior of windows and doors among others . Weather, population density, geographical distances, and local housing architecture play a role in the use of modular construction for home building.
Offices, hospitals, schools, retail centers -- modular building methods are the future of commercial construction. Living in coastal areas also mean that the modular home structure should be strong enough to withstand winds with high velocity. Modular homes, built correctly, have such kind of resistance to stand high wind velocity without any damage issues.